Robots and the Workplace of the Future this information to identify reusable components and strategic raw materials (IndustriALL 2015). Factory equipment will become increasingly digitised. In the smart factory model (also referred to as Industry 4.0), data is collected at each stage in the production process from sensors attached to machines or from existing digital interfaces. Data can then be aggregated and analysed in order to optimise the process. In many cases, process optimisation can be automated. For example, the trajectory of a robot arm, or its gripping force, can be adjusted automatically, with no human intervention, if the software determines this is necessary to minimise risk of damage, or speed up the production process. If a part from a sub-supplier is delayed, this information is automatically routed through to all of the other systems - from production planning to logistics - allowing for the necessary adjustments to be made at each stage. Inventory can be reduced through sensors on shelves and bins that send data on inventory status to inventory management systems. These systems can be set to trigger automatic orders of new stock if figures fall below set parameters. The data generated by linking machines to manufacturing systems can also be used to detect product defects and predict machine faults. For example, German manufacturer Daimler reduced the defect rate in cylinder head production by 50% in 16 weeks, leading to a productivity increase of 25% (IBM 2014). Predictive maintenance enables manufacturers to fix problems with machines before they occur. Previously, the equipment supplier would be alerted by the manufacturer only when the part was either due for a routine service (which it might not need), or was failing, resulting in machine downtime and production delays. Consultancy McKinsey estimates that predictive maintenance could save companies over $600 billion per year by 2025 (McKinsey 2015). Market research company IOT Analytics forecasts a compound annual growth rate (CAGR) for predictive maintenance of 39% over the time frame of 2016-2022, with annual technology spending on predictive maintenance reaching US$ 10.96 billion by 2022 (IOT Analytics 2017). Most manufacturers are investing in or acquiring companies that provide tools for collecting 7 and analysing data . Meanwhile, there is a growing market of Internet of Things software 8 companies , many offering services such as predictive maintenance, competing with equipment manufacturers doing the same. These developments in data capture, storage and analysis are generating new business models in manufacturing. The ‘servitisation’9 of parts of the manufacturing process that were previously performed in-house will, in future, extend to robots and potentially to entire manufacturing facilities (EFFRA 2016). Robot manufacturers are developing and commercialising service models based on data collected by sensors attached to robots. A number of robot manufacturers are working on ‘cloud robotics’ offerings which promise the 7 38% of manufacturers surveyed by the Economist Intelligence Unit in 2016 said they are investing in or acquiring technology companies (Economist Intelligence Unit 2016). See also (Financial Times 2017). 8 According to market research company IOT Analytics, there are now 450 internet of things platform companies (IOT Analytics n.d.). 9 Servitisation refers to the bundling of services with products. Products may be offered ‘as a service’ meaning customers lease the product rather than purchase it, with services such as maintenance and upgrades included in the leasing fee. March 2018 Positioning Paper 8
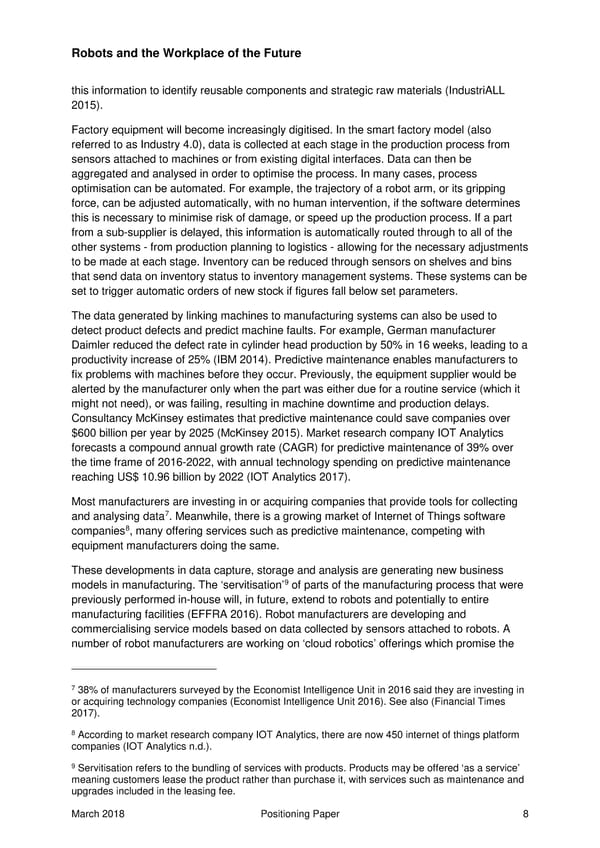