A positioning paper by the International Federation of Robotics Falling component prices, improvements in vision, gripping and mobility technologies combined with advances in artificial intelligence are leading to a growing market for collaborative robots6 that work alongside humans rather than being housed in cages. These robots are equipped with sensors and software that detect and respond to unexpected forces. Some collaborative robots, though not caged, remain fixed. Others are mobile, many with omni-directional wheels so they can move in any direction without having to turn. If a worker accidently bumps into a collaborative robot, it will either stop completely or move its actuator (a robot arm, or gripper for example) away. A mobile robot that moves around a factory or warehouse might be programmed to stop if its sensors detect a moving object within a certain radius. Importantly for SMEs, these robots can be programmed easily, often by guiding the robot manually through the action required. The combination of falling costs for robots and increasing adaptability enables SMEs to achieve productivity improvements without sacrificing the flexibility to work short production runs. Factories are becoming highly adaptive, able to switch production lines very quickly, enabling manufacturers to respond to customer demand for increased product variety and specialisation. The factory might be large, such as GE’s “multi-modal” factory which opened in 2015 in India. This factory can switch between production for GE’s oil & gas, aviation, transportation, and distributed power businesses as well as building products for a range of other industries. Conversely, many experts predict the dis-aggregation of manufacturing plants into small, highly versatile units that can be easily located close to demand. Manufacturing equipment will be modularised in units the size of containers, each containing a smart, internet-connected piece of manufacturing equipment, assembly robots, and test equipment. These units can assemble a variety of product orders from different customers who transfer product designs to licensed partners (Sol n.d.). A move to smaller manufacturing units could have a profound impact on the manufacturing market. In Europe, for example, large manufacturers dominate - about 1% of the internationalised, high- performing manufacturing firms in Europe produce more than 75% of output or foreign sales (Bruegel 2016) – and a move to smaller units could offer substantial opportunities for SMEs. The factory may be able to operate multiple product lines, or it may focus on one specific raw material, employing designers and sales staff and a small team of production planners, programmers and maintenance technicians who configure the factory in near-real-time for different orders based on that material (euRobotics aisbl 2014 ). European Trade Union IndustriALL believes a new ‘dis-assembly’ business model could create jobs and reduce waste. The dis-assembly model takes advantage of product tagging that is being used to steer and track products through the manufacturing life-cycle and uses dropped more than 25 percent since 2014 according to IEEE GlobalSpec's Engineering360 (Engineering 360 2017). BCG estimates that a combination of falling prices for robots, systems engineering and peripherals with increased performance translate into an annual 8% cost improvement for a typical application like spot welding ( BCG Perspectives 2015). 6 Market analysts forecast a rapid growth (between 50 and 60% CAGR) in the adoption of collaborative robots over the next 5 years – see (Research and Markets 2017), (MarketsandMarkets 2016), (Reuters 2016). The IFR is currently producing more definitive statistics for the uptake of collaborative robots and expects that market adoption may proceed at a somewhat slower pace over this timeframe. . 7 Positioning Paper March 2018
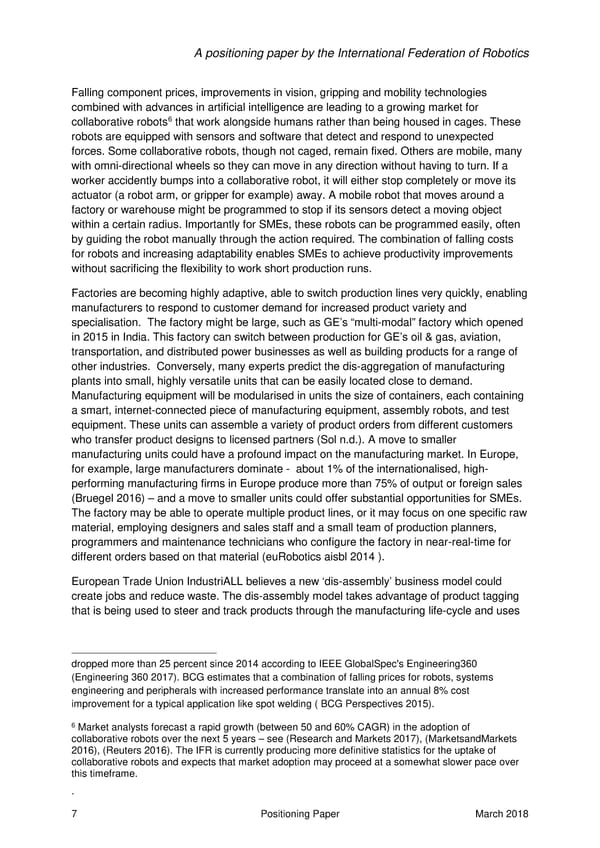