A positioning paper by the International Federation of Robotics automatic optimisation of robot performance by the robot supplier without intervention by the manufacturer. Data from robots at one or multiple customer sites can be aggregated and analysed to optimise a specific process. The robot programme can be adjusted and automatically downloaded back to one or all of the robots operating in the production step. The advantage of this ‘big data’ approach is that the more data optimisation algorithms are fed, the better their results. Research house IDC predicts that ‘by 2020, 60% of robots will depend on cloud-based software’ with 200% efficiency gains in being linked to a ‘mesh of shared intelligence’ (IDC 2016). Market research companies predict annual average growth in the cloud robotics market of around 30%, reaching between $ 22 and $ 36 billion by 2025 (Transparency Market Research 2017), (Research and Markets 2017). Some robot manufacturers are considering leasing rather than selling the robot, in a ‘Robot as a Service (RaaS)’ model. Customers pay for a continuously optimised robot that is programmed to meet their production requirements. This has clear advantages for SMEs; no initial capital outlay, fixed costs, automatic upgrades and no requirement for robot operators. IDC predicts that by 2019, 30% of commercial service robotic applications will be leased (IDC 2016). The advent of big data in manufacturing could redefine industry lines between equipment makers and manufacturers. For example, one Chinese robot supplier is becoming a manufacturer, setting up central robot manufacturing facilities in a number of provinces in China that will offer complete production services for a number of small manufacturing companies for articles such as furniture, sanitary ware and door handles. This model is being supported by a number of regional governments in China because it improves factory health and safety and enables easier and more accurate monitoring of emissions, reducing the load of monitoring thousands of small manufacturers to monitoring one that has better capital resources for addressing emissions. The impact of automation and robot adoption in manufacturing will be different in different economies. In ASEAN countries, which comprise over 600 million people, many of them manufacturing workers, automation is likely to lead to job or task displacement in some manufacturing sectors such as textiles, according to the International Labour Organisation. However, in electrical and electronics (E&E) manufacturing, one of ASEAN’s most prominent sectors and a mainstay of economic growth10 the trend is towards collaborative robots which support rather than displace workers. Because ASEAN’s E&E sector and subsectors possess a formidable and established nexus of producers and suppliers, the world’s high demand for IoT devices and components presents a significant growth opportunity (International Labour Organisation 2016). For all the promise of and hype around smart factories and Industry 4.0, progress is as yet relatively slow. Surveys by various management consultancies show adoption rates by manufacturers of robotics and automation of 15 – 37%, predicted to grow to around 50% over the next three years (PwC 2017), (MHI 2017). One issue hindering faster adoption is that large manufacturers run a huge number of different software systems, most of which are not compatible. Software systems of manufacturers, suppliers, and customers are rarely 10 .ASEAN’s E&E exports almost tripled over the past decade, reaching US $382.1 billion in 2014 according to the ILO. 9 Positioning Paper March 2018
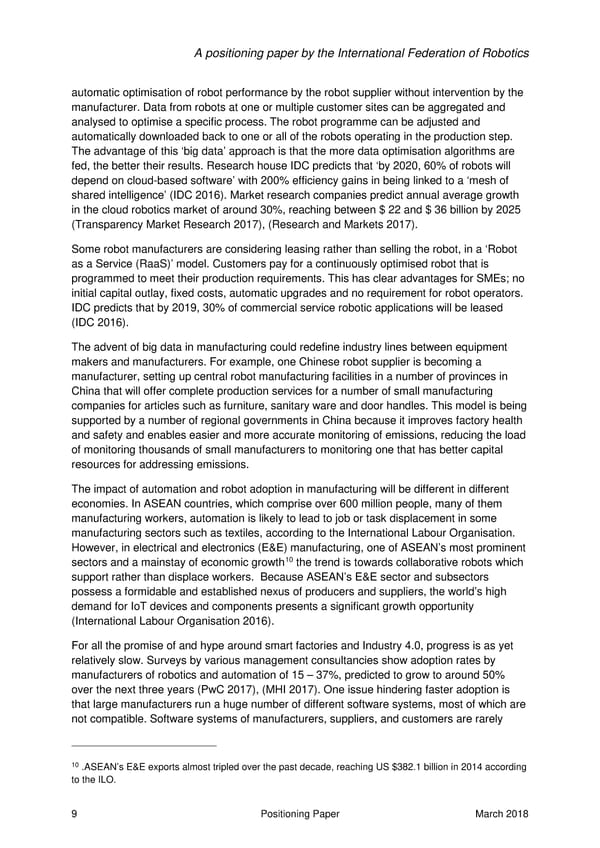