Robots and the Workplace of the Future closely linked. Nor are systems within internal departments such as engineering, production, and service integrated. Consultancy McKinsey estimates that more than half of the potential issues that can be identified by predictive analysis require data from multiple IoT systems that have not typically been required to share data and are frequently incompatible. (McKinsey 2015). Add to this the huge amount of data coming from sensors and it is not hard to imagine the complicated undertaking that implementing a connected factory model represents. Artificial intelligence programmes may help manufacturers address data incompatibility by enabling them to develop semantic maps – definitions of the information that is required by one system from another system. This would enable manufacturers to automate the extraction and conversion of that data throughout the factory (Manufacturing Business Technology 2017). Another issue, which we discuss in Section 3., is the fact that most manufacturers are still working out where it makes economic sense to automate. For SMEs, the economic viability of robot adoption is dependent on the ease of programming and operating the robot, not just on the initial capital outlay. The cost of software and systems integration accounts for between 60 to 75% of the total cost of robot ownership ( BCG Perspectives 2015) (IFR 2017). Robot manufacturers and researchers are focusing on developing intuitive programming interfaces modelled on consumer electronics. Some experts envisage a future of open robot applications platforms from which manufacturers can select applicable programmes (Fraunhofer IPA 2016). ROBOTS IN LOGISTIC S Automation in logistics has traditionally focused on highly standardised processes such as ‘goods-to-picker’ models that work with standard pallet sizes and marked routes. Advances in vision and gripping technologies are now expanding the application of robots into non-standard environments. These include picking individual items and loading trucks with parcels of different weight, shape and robustness. Robots will increasingly assume unergonomic, ‘heavy-lifting’ tasks within logistics, freeing humans to focus on managing operations. ‘Last-mile’ deliveries from the last logistics centre to the end customer are being automated though autonomous terrestrial delivery robots which are being tested in a number of countries. Legal hurdles with drone delivery may be overcome at sea sooner than on land. Logistics is a huge11, capital intensive and highly competitive market yet aside from notable exceptions such as amazon, the extent of automation is still low12. While robots have been used for some time in warehouses to load pallets of goods on and off trucks and move them within factories, their use has largely been limited to standard shapes and routes. Goods-to- 11 Estimates of the size of the logistics market vary between $ 2.7 and $ 8.1 trillion (Transparency Market Research 2016 ). 12 For example, supply chain consultancy St Onge estimates that 80% of warehouses are manually operated with no supporting automation (DHL Trend Research March 2016) while a survey conducted for Modern Materials Handling found that only 20% of over 200 companies surveyed used robots for palletizing or picking, and only 10% used mobile robotic storage and retrieval systems (Modern Materials Handling 2017). March 2018 Positioning Paper 10
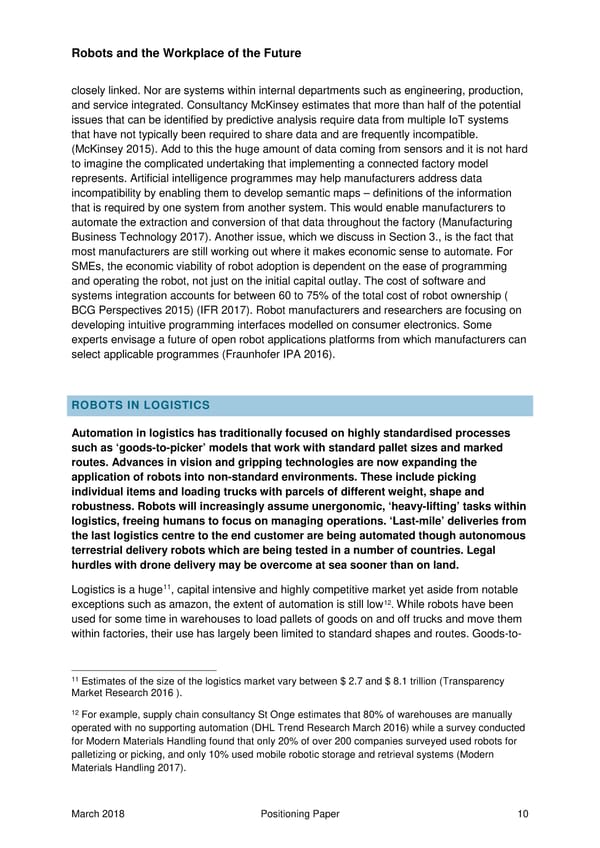