A positioning paper by the International Federation of Robotics good communications skills a pre-requisite. They will need to be adaptable and apply a wider range of skills in their roles. Skills requirements will not be static, rather each worker will need to evolve their skills to fit a range of projects. The impact on skills requirements in healthcare will be less dramatic. The main use of robots in this field will be to reduce heavy, monotonous and fetching-and-carrying tasks for nurses and carers, freeing them to spend more time on patient interaction. Nevertheless, new skills in operating robots will be required, and will be more demanding in areas such as rehabilitation where the robot or robotic device must be programmed to the needs of the individual patient. Carers will also need to adapt to the use of virtual (telepresence) robots to interact with patients. Digital skills will be key in all industry sectors. Approximately 50% of automotive respondents in a study by Boston Consulting Group (BCG) of more than 750 production managers from companies in the automotive, engineered products, and process industries, said that they expect to employ more workers with IT skills, and approximately 25% expect the number of IT employees will increase by more than 10% (BCG 2016). The European Trade Union Institute predicts the increase of jobs such as data analysts, miners and architects, software and application developers, specialists in networking and artificial intelligence, designers of robots, 3D printers and other ‘intelligent’ machines, as well as digital marketing and e- commerce specialists (European Trade Union Association 2016 ). All of LinkedIn’s top 20 ‘hottest skills of 2015’ were digital (European Political Strategy Centre 2016). The focus on digital skills is leading to a variety of new jobs types, at all levels, from robot programmers and mechatronic engineers to Chief Digital and Chief Robotics Officers18. IT skills alone will not meet the requirements of smart factories and warehouses, however, or be enough to optimise processes in hospitals. One quarter of managers in the BCG study expect to need people with production planning and logistics skills. The focus on job profiles combining digital with production, process and operations planning skills is reflected in a number of other studies (Dutch Ministry of Economic Affairs et al. 2014), (VDMA 2016), (BCG 2015). And although IT skills are in short supply (as we’ll discuss in Section 4.), in- depth process knowledge may be ultimately more valuable in many companies. A number of companies interviewed for a study by the German Mechanical Engineering Industry Association preferred to train their production specialists in IT skills than to train their IT specialists in production processes, reflecting the importance of tacit knowledge that comes from process experience on the job. As one interviewee put it, ‘Big Data works perfectly if you have a complete understanding of the underlying processes, but if you don’t know what effect you are trying to observe, you won’t have your sensors in the right places and you won’t be able to collect the data you would need to analyse that effect correctly’ (VDMA 2016). The importance of technical expertise is not limited to advanced economies. In a survey of 4000 companies in the ASEAN region by the International Labour Organisation, 18 Recruitment agency Russell Reynolds Associates says that in Europe, the number of search requests for a Chief Digital Officer has risen by almost a third in the last 24 months. The United States has seen the same growth in half that time (Russell Reynolds 2017). IDC predicts that by 2019, 30% of leading organizations will implement a chief robotics officer role and/or define a robotics-specific function within the business (IDC 2016). 17 Positioning Paper March 2018
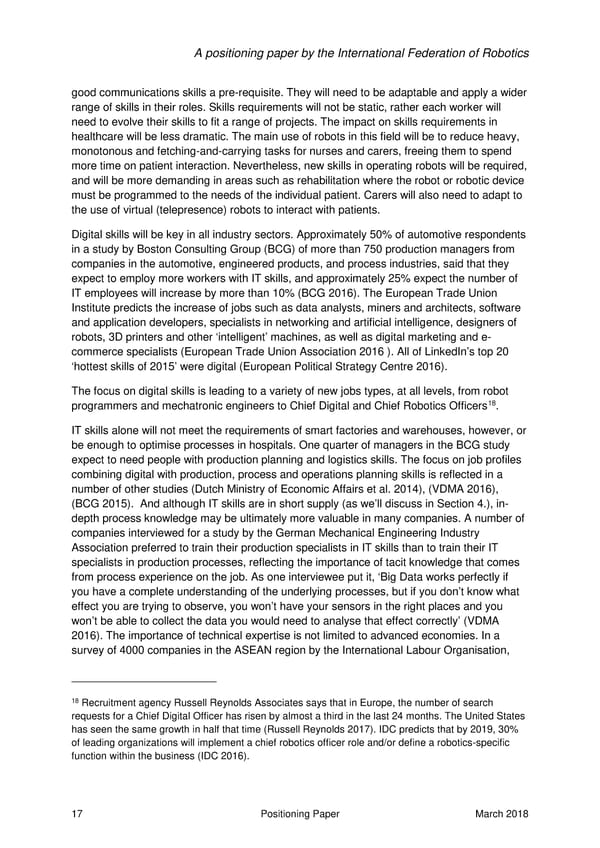