Robots and the Workplace of the Future 3. ROBOTS, AUTOMATION AND THE WORKPLACE OF THE FUTURE Automation is changing job profiles. This section focuses on the skills requirements for new job profiles. We discuss the consequences for organisational and management structures, and skills requirements. Robots, as part of broader automation strategies, are set to have a substantial impact on productivity, business models and even traditional industry boundaries and, as a result, on work. Much of the narrative on the impact of automation on employment and jobs focuses on scenarios in which entire job profiles and professions – including white collar professions - disappear. In our paper The Impact of Robots on Productivity, Employment and Jobs we reviewed current evidence and thinking on the impact of automation on employment and jobs. Most research by academics and consultants concludes that automation does not lead to net job destruction, and that very few (less than 10%) of jobs will be replaced through automation in the foreseeable future. Rather, it will be tasks that are automated, with workers taking on new tasks that result in higher-skilled, higher-paid job profiles. JOB PROFILES AND SKILLS REQUIREMENTS Digitalisation and automation are changing job profiles and skills requirements. Robots will take on an expanding range of routine, repetitive tasks, many of them sources of chronic injury. In general, workers will increasingly focus on unstructured tasks such as managing production flows, resolving exceptions and bottlenecks and dealing with customers or patients. New job profiles will generally be higher-skilled, better paid and give workers more autonomy. However, workers will also continue to perform routine tasks, either because it is not economically viable to automate them, or because automation has created new routine tasks that require human skills. Employers will place increased emphasis on ‘soft’ skills such as problem-solving, decision-making under pressure and communication. Digital skills will be key in all industry sectors. New job profiles are likely to contain a strong digital element. However, process expertise will remain highly prized and takes longer to acquire than digital skills. Manufacturers may find it easier to train production specialists in IT than vice versa. Assistive systems, including virtual reality, will support workers in learning and performing tasks. Robots and assistive systems will increasingly be used to support healthcare workers in patient rehabilitation and elderly care. Wearable robots including exoskeletons will be used across a range of industries to prevent chronic injuries and support workers and patients with restricted mobility. Increasing adoption of robots, as part of broader automation strategies, will change job profiles and skills requirements. The European Factories of the Future Research Association, for example, predicts that manufacturing workers will no longer perform routine tasks. Instead they will have to perform varied and mostly unstructured tasks, depending on the needs of the dynamically changing production process (EFFRA 2016). Workers will be tasked with controlling, and sometimes programming, robots and other automated processes, and managing production flows, stepping in manually when there are exceptions to a planned process. The same task and skills-set applies to logistics (DHL Trend Research March 2016). In most cases, workers will be part of multi-disciplinary project teams, making March 2018 Positioning Paper 16
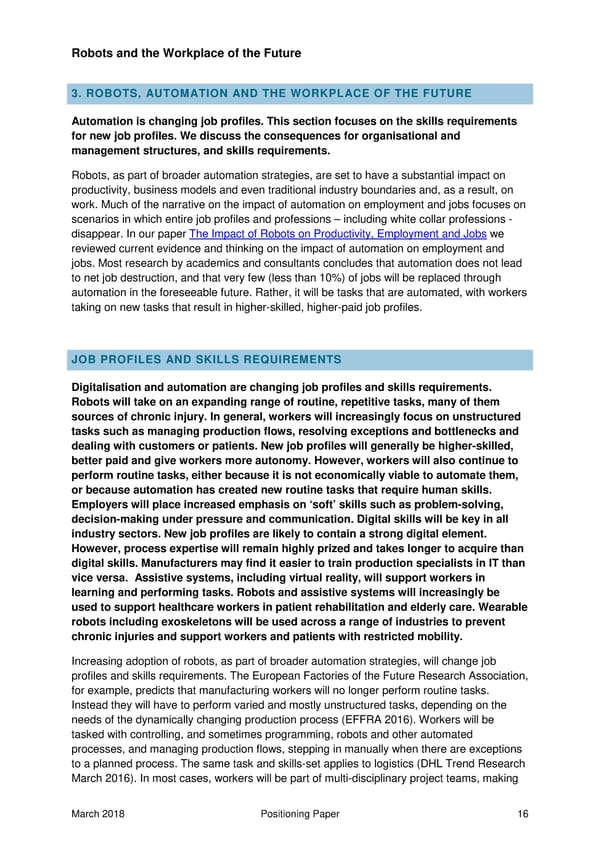