Robots and the Workplace of the Future technical knowledge was considered the most valuable skill, followed by teamwork and communications skills (International Labour Organisation 2016). In their drive to establish leadership as producers of IoT devices and components, ASEAN’s electronics manufacturers will seek higher skilled talent with R&D competencies, ranging from analytical experts to autonomous driving engineers and sustainability integration experts. Some tasks will be carried out by workers remotely rather than directly. For example, crane drivers at shipping and transport company Maersk’s Maasvlakte II terminal in Rotterdam now work as ‘remote operators’, moving the cranes from inside a control room using six screens showing multiple camera angles with the ability to zoom in anywhere for a closer look (Maersk 2015). Robots will continue to take on routine tasks that are either hazardous, or unergonomic, leading to chronic physical complaints. Welding, for example, is extremely hazardous to the human body19. Robots are also being used for routine cleaning tasks in hospitals and government buildings that may have hazardous or contaminated environments20. Workers will increasingly use digital tools for training and support in executing tasks. For example, maintenance technicians who previously carried a phone and a computer with a limited technical database will in future be equipped with cameras, geolocation systems and online access to a full database of technical data. The technician can take photos that are processed by algorithms that identify the photographed part and provide access to relevant information. The technician can see a full maintenance history of the part and can place an order for replacement components. He or she can send an estimate for the repair directly to the client, who can sign off digitally, triggering the automatic generation of an invoice (European Trade Union Institute 2016). EFFRA and other experts predict the increased use of augmented reality technologies for carrying out tasks and for training. For example, maintenance workers may receive repair instructions on how to replace a particular part as they are looking at the actual system needing repair. This information may be displayed directly in workers’ field of sight using devices such as augmented-reality glasses. Large industrial companies are already using virtual reality simulation to train plant personnel to handle emergencies (BCG 2015). EFFRA predicts the increased use of wearable embedded equipment connected wirelessly to the surrounding manufacturing environment to alert workers to potential safety or ergonomic hazards (EFFRA 2016). E-learning courses, addressing specific issues faced by workers on the job, will also be increasingly available (Fraunhofer IGCV 2017). All the literature on skills requirements of the future shows a clear trend in manufacturing and logistics away from routine tasks towards work that is more varied, more satisfying and 19 Dangerous fumes from metals and coatings can lead to serious illnesses. Some products contain lead or asbestos, and the exposure can lead to emphysema, lung disease and even kidney failure. Along with the fumes, manual welding produces a lot of noise and intense heat. The loud environment can cause hearing loss of stress in the welder, and the heat can cause burns or heat exhaustion. The ultraviolet light from the welding torch can cause Ultraviolet Keratitis, also known as “welder’s flash”. 20 For more examples of the dangerous tasks that robots perform, see https://www.robotics.org/blog- article.cfm/Dangerous-Robot-Jobs/15 and http://www.webdesignschoolsguide.com/library/10-things- we-couldnt-do-without-robots.html. March 2018 Positioning Paper 18
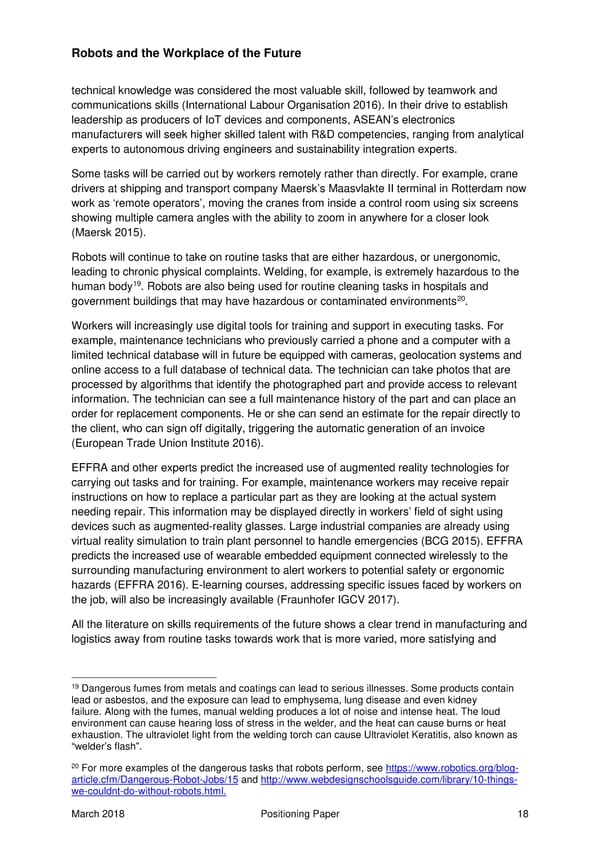