A positioning paper by the International Federation of Robotics Meet the new co-worker Some workers in smart factories and warehouses, and in hospitals and care facilities, will be responsible for robot operations and the effective integration of robots into processes and workflows. Others will be working directly with robot co-workers. Logistics provider DHL, for example, sees a future in which robots and humans work together in a co-packing area to assemble basic products or components into new items customized for individual orders (DHL Trend Research March 2016). Collaborative robots, that can sense their environment and either stop or move away when humans approach, will perform a wide range of tasks in factories and warehouses. They can work with humans to lift heavy weights from one position to another, for workers to then process; fetch and carry parts needed by a worker in a process; and perform high-precision tasks in an assembly process that is driven by the worker. Collaborative robots can glue, weld, solder, mark and label products and perform quality control by recognising non-standard items. The International Standards Organisation identifies four types of human-robot collaboration. These range from coexistence, where a human and a robot work alongside each other but do not share a workspace, to collaboration, where a human worker and a robot work simultaneously on the same product or component. The Fraunhofer Institute found in a study of 25 German manufacturers that the coexistence model prevails, with genuine collaborative applications virtually non-existent currently in production facilities. Considerable research is going into collaborative applications in which robots interpret and respond to human voice, gesture and movement. For example, if a robot and a human are to successfully carry an object together, the robot has to adapt its motion to compensate for the pushing and pulling forces exerted by the human via the carried object (Berger, Vogt and Haji- Ghassemi 2013). Artificial intelligence will allow robots to anticipate and react to the specific requirements of individual workers – for example, identifying if they are left or right-handed and adjusting the path of the actuator accordingly (EFFRA 2016). One research project in medical applications, which require particularly accurate motor coordination, looked at the optimal selection, picking and handover of surgical instruments from a speech- and gesture-based robotic nurse to a surgeon in an operating theatre (Jacob 2013). In some cases, workers will not just be working with a robot, they will be wearing one. Exoskeletons will be used to enable workers to deal with heavy loads without injury. Exoskeletons can reduce the incidence of chronic back conditions due to long periods of being in one position. ‘Wearable seats’ - lower-limb exoskeletons that enable factory workers to assume a sitting or semi-sitting position when required – are being tested by a number of car manufacturers to reduce lower-back strain (SPARC 2016). Researchers at MIT are working on an exoskeleton that attaches to the hips and provides additional arms or legs, depending on the wearer’s requirements. These exoskeletons improve productivity* and mean workers do not have to assume unergonomic positions to complete tasks (RoboHub n.d.). * The impetus for the development of the MIT exoskeleton was an observation that for some tasks in aircraft assembly, two or three workers collaborated on the same task, but only one of the two or three was doing the important task - for example drilling – with the other two carrying out boring and tiring tasks like lifting parts or following the first worker with a vacuum cleaner. 21 Positioning Paper March 2018
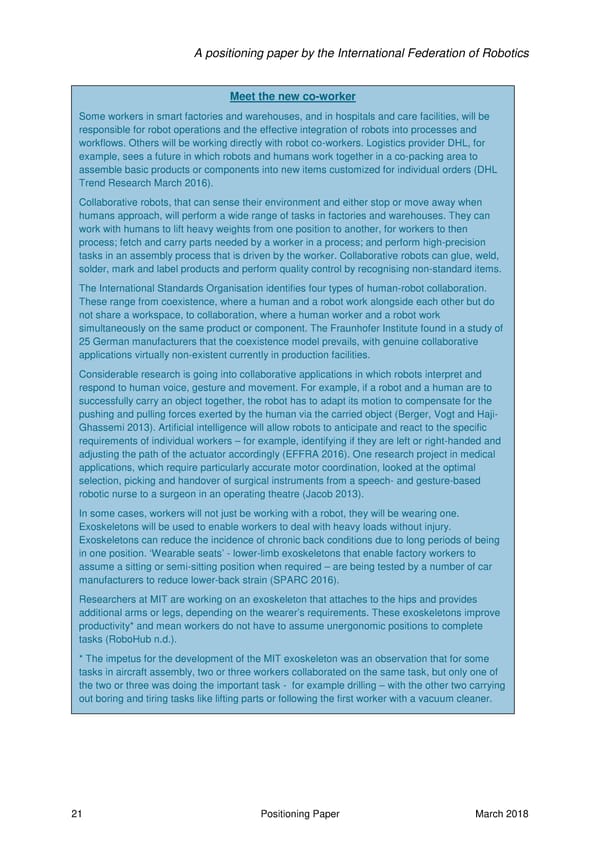