Robots and the Workplace of the Future ORGANISING WORK: HUMANS IN THE LOOP Robots will not replace humans. Indeed, people are central to successful automation strategies, particularly in the challenging environments described in Section 2. Increasing adoption of collaborative robots is changing the nature of human-machine interaction. Companies must focus on designing processes to use people, machines and IT most effectively. This will become a source of competitive advantage. ‘Will human workers in the smart factories be turned into tools of tasks decided by robots and their algorithms? Or are the machines the workers’ partners? Will we see an ‘emancipation’ of workers from routine and repetitive tasks? Or a restriction of workers’ room for manoeuvre or even free will?’ asks the European Trade Union Institute (European Trade Union Association 2016 ). Trade unions in Europe are generally positive about the potential of automation for higher- skilled, higher paid and more satisfying jobs, but all stress the need for workers to be involved in process design and the importance of continuous training and up-skilling (European Trade Union Association 2016 ), (Trades Union Congress 2017). Most experts believe humans will remain central to work processes in the industries we have discussed in Section 2.25. As Acatech, the German national academy of science and engineering, points out, ‘Systems can be set up to impose restrictive control over every minute detail of a person’s work, or they can be configured as an open source of information that employees use as a basis for taking their own decisions. (…) the quality of people’s work will not be determined by the technology or by any technological constraints but rather by the scientists and managers who model and implement smart factories’ (Acatech 2013). Studies indicate that workers in productive smart factories and warehouses could enjoy more, not less, autonomy as a result of automation – but companies must design processes with this goal in mind. For example, a German manufacturer that introduced advanced machining systems to manufacture components ensured workers retained autonomy by giving them product specifications and allowing them to decide how to best use automated systems (European Trade Union Institute 2016). In low-volume, high-mix production environments, companies must be able to rapidly switch between different types of product run. Most experts believe this will result in a move to decentralised management structures in which project teams are given a high degree of autonomy to make decisions in real-time based on changing project requirements and conditions (EFFRA 2016), (Technische Universität Dortmund 2016). Teams will assemble ‘on the fly’ to provide the required skills for a given project and then re-configure for the next one. These teams are likely to be multi-disciplinary and combine workers of different age-groups and experience levels who will work together remotely as well as in person. 25 For example, more than three-quarters of respondents in a survey by SCM World with MESA International believed that people will be at the centre of the automated factory of the future, because they provide the degree of flexibility and decision-making capabilities required to deal with demanding customers (SCM World 2014). March 2018 Positioning Paper 20
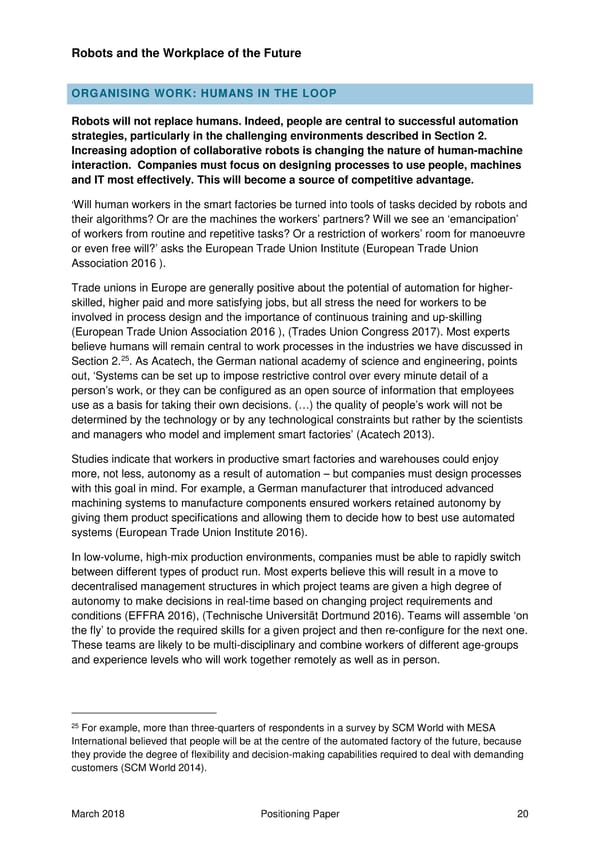