A positioning paper by the International Federation of Robotics schemes. Most experts see industry alliances, of which there are an increasing number, as the most effective path to address skills gaps on an industry-wide basis. Industry skills alliances mean educational institutes know their investment reflects the needs of an industry sector rather than one or two specific employers and enable small businesses to benefit (National Skills Coalition 2017). The U.S. has a number of these initiatives, some nationwide and some regional. On a nationwide level, the ARM Institute, a public-private partnership funded by the Department of Defence, develops education and certification programmes and supports semi-autonomous regional centres that collaborate with local manufacturers. A successful regional example is RAMTEC, formed in Marion, Ohio to supply skilled workers to local manufacturers. RAMTEC works with robot manufacturers to develop certification and associated training programmes that will enable students to find jobs more easily. In Europe, the Academy Cube, an initiative between international industrial companies and public institutions, specifically targets skilled workers from southern Europe, where unemployment rates are particularly high. The Academy Cube offers unemployed graduates in ICT and engineering the opportunity to obtain targeted, and certified qualifications and helps put them directly in touch with industrial enterprises (Acatech 2013). The World Economic Forum has launched a Closing the Skills Gap Initiative aimed at encouraging companies to commit to investments in skills training (World Economic Forum 2017). Efforts to standardise skills and credentials would enable better communication between companies and higher education institutes. In ASEAN countries, where education systems are often based on outdated curricula and rote learning and where there is a lack of certification frameworks for technicians, manufacturers such as Mercedes-Benz are offering technical apprenticeships using a dual-education system to meet a need for engineers with specialized knowledge of automated process design and robotic programming. Mercedes- Benz partners with a vocational school accredited by the Ministry of Education in Thailand and has also established a training centre in Indonesia (International Labour Organisation 2016). Increased public-private sector collaboration is important not only at the level of educational institutions, but also at government level in order to strengthen policy. An OECD review of vocational training programmes, for example, found that although Korea has a strong vocational education training (VET) programme system, weak industry links at government level meant that policies were not being developed to help the VET system adapt fast enough to changing labour market needs (OECD 2015). FUNDING INVESTMENT IN HUMAN CAPITAL Experts agree that more investment in human capital is needed to close the current skills gap and ensure that workers can benefit from advances in automation. The question is who will pay – government, employers, employees, or a combination of all three? Many companies invest substantially in human capital development, but between one third and one half do not. The increasing use of flexible work arrangements such as agency contractors and short-term employment contracts disincentives investment in human capital in sectors and companies that make heavy use of these arrangements. Research shows that companies that use technology effectively enjoy substantial competitive advantage. In the age of automation, 25 Positioning Paper March 2018
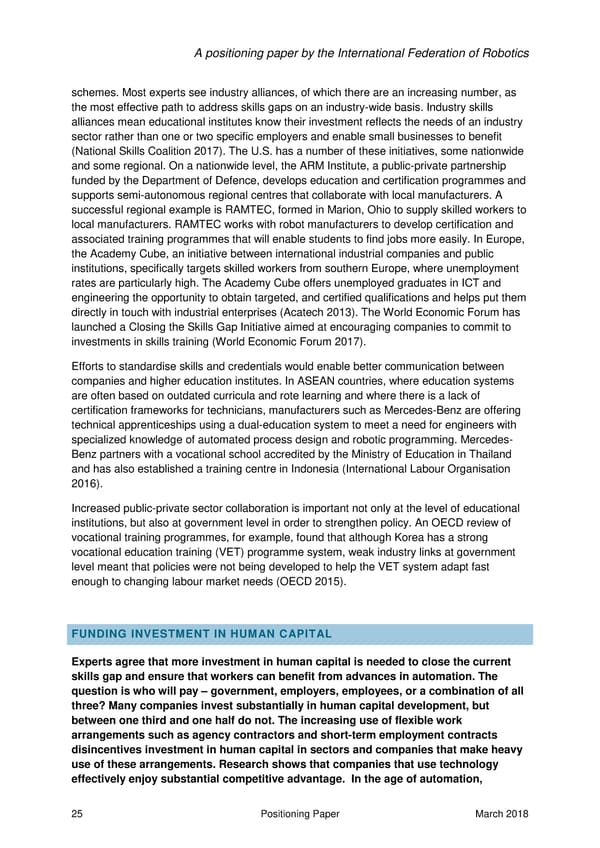