5. A study of four sectors 34 5. A study of four sectors To develop a more compelling picture of the robotics One example is the increased adoption of cobots for landscape we have selected four sectors in which robot transportation purposes in collaborative environments. and cobot solutions have been applied at varying Just as the first industrial robots were installed away scales. We will consider each of the sectors across the from humans in factories and laboratories, the first medium term (up to three years). vehicular robots were found in warehouses where they could be used to manipulate larger payloads or Industrial dexterously configure smaller quantities of merchandise. We are now seeing more transport Robots are commonly used in industrial environments cobots operating in closer proximity to humans with due to their ability to perform operations and processes mobile robots used in a range of applications, extending quickly, repeatedly and accurately. Traditional industrial the concept of Automatic Guided Vehicles (AGVs) to robots are used for fabrication processing, foundries, Autonomous Mobile Robots (AMR) (Schneier & welding, painting, coating and sealing, flexible fixturing Bostelman, 2015). The difference now is an important and workpiece handling, as well as material handling one. Whereas the standard AGV, which has been and warehousing, assembly of mechanical and around for almost 50 years, follows fixed routes, the electronics, quality assurance, maintenance and repair robotic AMR uses sensors and on-board computers to and re-manufacturing (Nof, 1999). In addition to understand its operating environment and dynamically traditional robots operating in ‘caged’ or highly- navigate using a map. controlled environments, there is increasing deployment Cobots in collaborative environments must be designed of smaller, lighter cobots within both SMEs and large to minimise safety concerns. Important design factors manufacturers, in environments where they are close to (Kildal et al 2018) include proximity detection systems or interacting directly with humans. As the Loup that slow down or stop movement, and collision Ventures report indicates, the market for these robots detection systems that operate through force- or torque- will continue to grow at a rapid rate due to increased sensing in the robot’s joints, enabling subsequent labour costs and the need to avoid dirty, dangerous and reaction to that collision. Another safety factor difficult jobs (Murphy, 2017). (according to Interviewee #9) is hand-guiding where the Robots, cobots and mobile devices are increasingly robot is under the direct control of an operator. This being developed for industrial tasks outside the requires sensor and actuator systems that enable the traditional factory environment. Interviewee # 6 pointed robot to be physically manipulated by the user without resistance. Also important are a projection-based space to over £90m of funding by the UK’s EPSRC into four major centres for robotics research outside of the monitoring system, safety zones around the cobot’s factory. immediate area of influence and variable stiffness in actuators (Kildal et al, 2018). Taking control: robots and risk
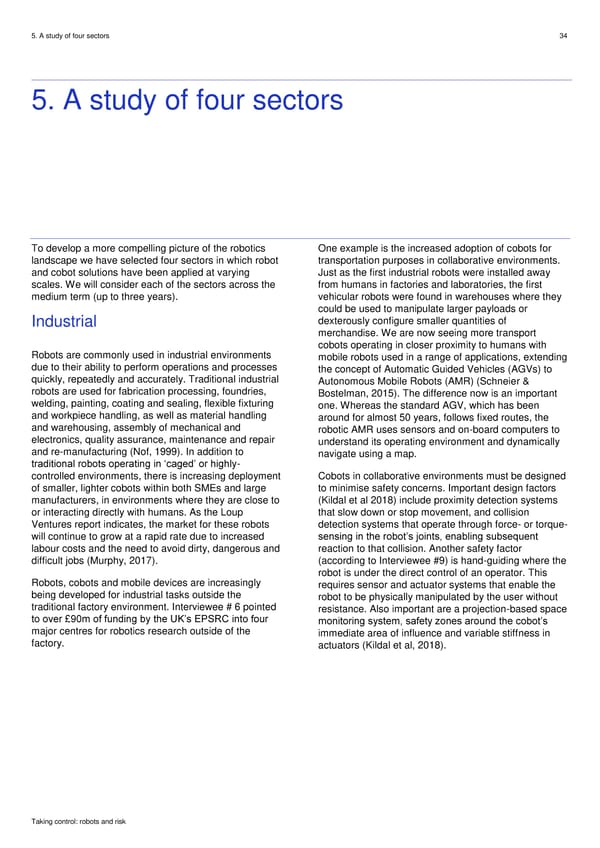